How to Choose the Right Ergonomic Platform trolley for Your Facility
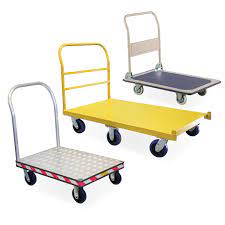
A national third-party logistics provider experienced recurring congestion in its batch-picking zone, where workers traveled long distances to consolidate orders. When equip2go Platform trolleys, fitted with adjustable shelving and ergonomic handle kits, were introduced, the company reported a 35 percent increase in orders processed per shift. There was reportedly a 50 percent reduction in lower back discomfort in operators, leading to fewer mid-shift breaks and a heightened focus on quality checks. The responsive wheel systems on the trolleys navigated narrow aisles with ease, and the quick-attach shelf modules allowed for rapid recalibration for different client SKUs. The facility recouped its investment in three months, the company said, through freight cost savings due to quicker order fulfillment and fewer need for temporary staffing during peak seasons.
Selecting the platform trolley
When selecting an ergonomic platform trolley Brisbane, a thorough evaluation of facility layout, product profiles, and workforce demographics is of paramount importance. Important aspects include height-adjustable handles, to suit the average operator height, platform size to suit common load dimensions without overhang, and tire compounds that suit the flooring material to provide reliable traction. equip2go takes a consultative approach with customers through this process, using site surveys and usage simulations to suggest models that strike the right balance between capacity, maneuverability and ergonomic fit. The interfaces simplify integration with other systems, while spring-assisted deployable shelves, electric drive modules, or vibration-dampening caster assemblies provide a high degree of flexibility in adapting the Platform trolley to your specific operational requirements. Choosing the right combination enables organizations to maximize initial adoption and long-term productivity benefits.
Employee Training, and Implementation Strategies
Making efficient use of the ergonomic Platform trolleys goes beyond simply purchasing the equipment; it requires effective training and change management. In this way, to maximize the ergonomic features, it is necessary that employees are trained in proper posture, selection of handles, and distribution of loads. equip2go offers examples of best practices, from quick-start guides to on-site workshops—such as how to keep clear lines of sight when pushing trolleys and locking wheel brakes before loading. Supervisors are key to strong reinforcement of safe use, carrying out regular audits and obtaining operator feedback for possible ergonomic improvements. Continuing support will make sure that in case of unwanted workaround or misuse, this will be resolved as soon as possible and no safety benefits or productivity increases will be lost on the Platform trolley fleet.
ROI and Future Value
We have seen that ergonomic Platform trolleys generally come at a premium price compared to the most basic carts. However, compared to the long-term value of these tools, these initial cost differentials are relatively modest. The prevention of worker injuries reduces organizations’ medical claims and leads to reduced insurance premiums. The robust build of equip2go trolleys, along with modular components (that can be upgraded or replaced) extends service life well past a decade in many cases, reducing capital costs in the long-run. When determining total cost of ownership—factoring in labor savings, safety improvements, and productivity uplifts—the payback period for returns on investment for an ergonomic trolley often only takes a few months; a positive return that makes investing in ergonomic trolleys a strategic necessity in order to succeed in warehouses competing against one another.
Ergonomic Design Trends for Platform Trolley
Ergonomics and sustainability will also drive the design of Platform trolleys as material handling continues to evolve under the effects of automation and data analytics. New trends include embedded sensor networks that quantitatively measure push/pull forces in real-time feed these data to managers so that they can intervene before an injury becomes a reality. equip2go has launched pilot initiatives with IoT-capable trolleys sending usage data to centralized dashboards for proactive maintenance and ergonomic audits into the design of systems. To further reduce the trolley mass without compromising load capacity; in turn, this reduces the force needed to set it in motion, lightweight composite materials are also being investigated.